How To Generate Electricity Without Burning Natural Gas
November 7, 2024
Across the globe, millions of miles of transmission and distribution pipelines deliver natural gas to power cities, factories, and homes. When the gas in these pipelines is burned—whether to spin a giant turbine or heat an afternoon pot of tea—CO2 is released into the atmosphere, further unbalancing our planet’s already out-of-kilter carbon cycle.
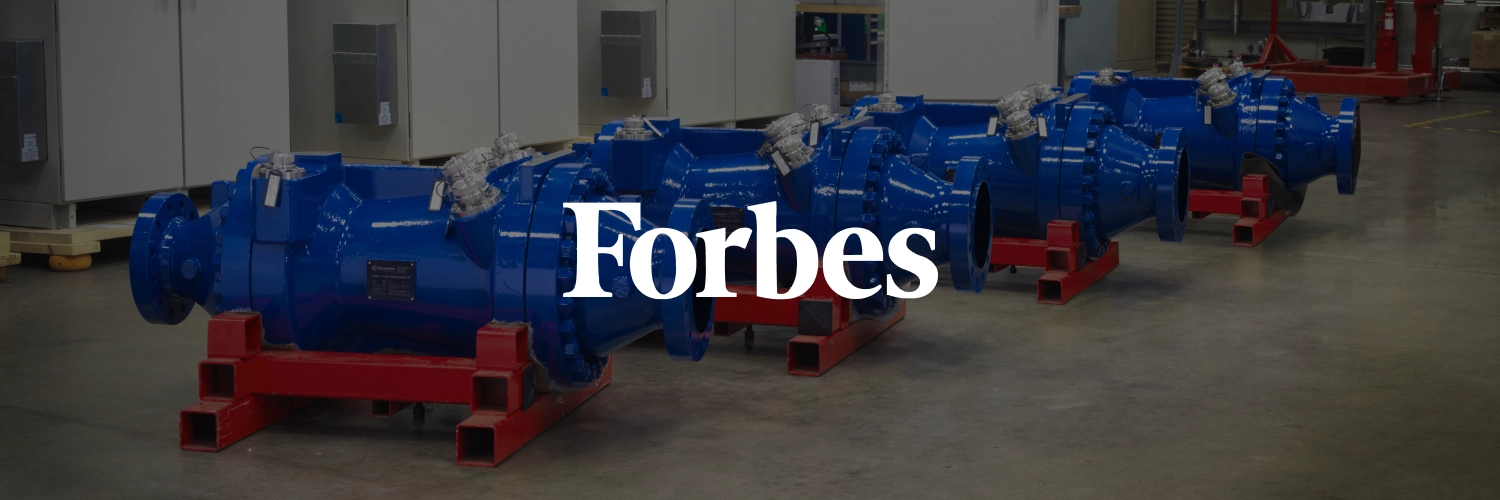
Imagine my surprise when I learned that natural gas need not be burned to generate electricity. Two American companies—Sapphire Technologies, a West Coast spinoff of Calnetix, and Anax Power, a private East Coast company—have modernized an industrial device called a turboexpander to transform natural gas pipelines into miniature zero-carbon power plants.
Think about how strongly a beachball springs up after you force it underwater. The same release of energy occurs in natural gas pipelines; whenever gas pressure is reduced, the pressure differential can be used to produce electricity without burning any fuel.
Burning less natural gas is the first best approach to reducing atmospheric CO2 levels. However, since civilization continues to use natural gas, a single turboexpander can generate several gigawatts of electricity—enough to power the equivalent of over two million households.
As turboexpanders can be installed at hundreds of thousands of pressure letdown stations along natural gas pipelines, one industry executive with whom we spoke believed this technology could generate fully one-fifth of U.S. electrical demand.
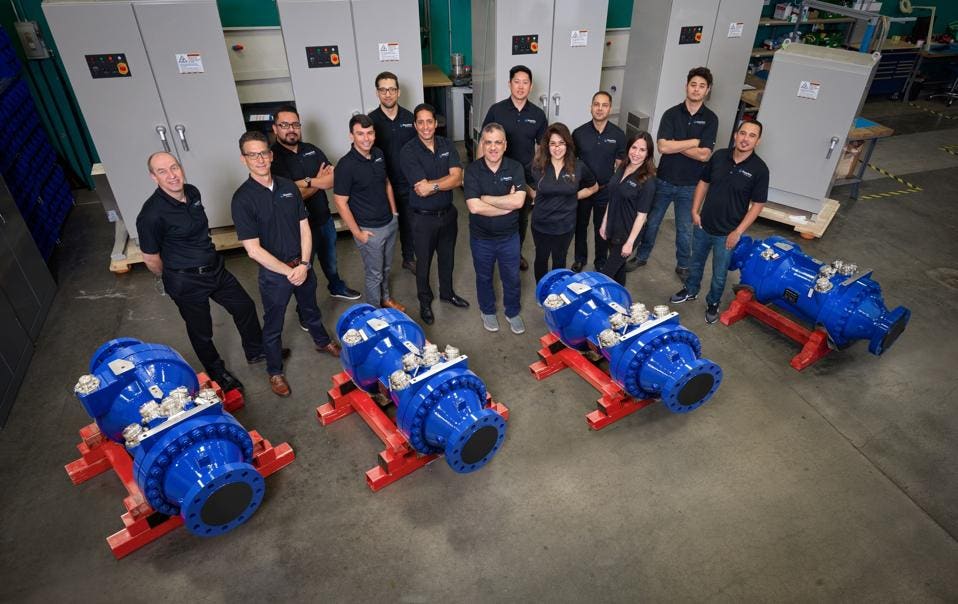
Generating zero-carbon electricity from natural gas using “waste pressure”
Turboexpanders were invented years ago to recover energy at petrochemical plants. Whenever the pressure of a gas is reduced—such as when natural gas transitions from high-pressure transmission lines into lower-pressure distribution systems, or when LNG is offloaded at a port—energy is released. Turboexpanders can harness changes in pressure to spin an electric generator instead of letting that energy go to waste.
Turboexpanders are widely used in petrochemical plants, where operating conditions are highly controlled and equipment can be inspected and maintained regularly.
Pipelines, on the other hand, operate with much less stability—sometimes gas comes through at high pressure, sometimes at a lower pressure, and sometimes not at all. Junctions where pressure is let down are often remote, so equipment cannot be maintained as easily. These complications led to the failure of a major pipeline company’s turboexpander generator pilot in 2004.
.jpeg)
Sapphire Technologies and Anax Power have modernized legacy turboexpanders by replacing mechanical bearings with magnetic ones, sealing the device’s housing, and developing improved variable-speed drives to adjust for changes in pipeline gas pressure. These changes allow turboexpanders to function with less frequent maintenance, enable them to handle changing operating conditions, and improve safety.
Multiple turboexpanders can be installed together, each capable of generating substantial amounts of electricity. However, one limitation remains: The electricity generated must be delivered to a load. This presents a challenge, especially at remote locations where building out electrical infrastructure can be prohibitively expensive.
Solving the electrical distribution problem
Apropos to companies generating electricity by not burning natural gas, both Sapphire and Anax have solved the logistical problem of distributing electricity by not distributing it.
Developers do not mind building power-hungry data centers in remote areas where turboexpander generation is possible, so electricity generated from waste pressure can immediately be put to work. Waste heat from data centers can be used to warm the pipelines at pressure reduction junctions, which is conventionally done by burning some of the gas.
Anax has already built and installed a turboexpander in rural Pennsylvania, and is pursuing deals to build more. Meanwhile, Sapphire has partnered with Tallgrass (a pipeline company) and Evolve (a data center developer) to establish a network of 72 turboexpander-powered data centers in the U.S.
.jpeg)
If pressure let-down junctions are located close to electrical tie-ins, power can be delivered to the grid. Sapphire installed its first unit at a site in Italy where a pressure release junction was close enough to an electrical tie-in to provide power to a town. Its most recent pilot project, at a liquified natural gas terminal in Japan, operates in a similar way.
The business of turboexpanders
While both Sapphire and Anax are solving the same problem with a similar product, Sapphire looks further along the commercialization pathway.
Sapphire was spun off from Calnetix Technologies, a company that designs and produces small runs of highly specialized or innovative products, especially high-speed rotating equipment and turbomachinery. For example, NASA is using a Calnetix carbon dioxide scrubber on the International Space Station.
The Italian turboexpander generator mentioned above was built as a pilot on behalf of a large oil and gas client; upon the pilot’s success, Calnetix management saw the potential to build a larger business around that device. Calnetix stood up Sapphire as a separate company and sent two executives, including CEO Freddie Sarhan, to build a business around the innovation.
In 2021, Sapphire raised $10 million in a Series A funding round, including investments from Chevron, Equinor, and Cooper & Company. This initial capital enabled Sapphire to develop its flagship technology and complete the pilot installation at the Japanese terminal.
Building on this momentum, Sapphire secured an additional $10 million in Series B funding in 2023 led by Energy Capital Ventures. This round included participation from Marathon Petroleum, as well as its earlier investors. The funding is being used to increase production capacity and extend Sapphire's market reach, including its partnership with Tallgrass and Evolve Energy. Sarhan believes that Sapphire technology can be used at each step in the natural gas transport chain: Wellhead pressure must be stepped down before gas enters the transmission system and stepped down again before gas enters the distribution system.