Hydrogen Gas
Hydrogen is a rapidly expanding global energy storage market. Hydrogen is used in many manufacturing processes from petroleum refining to food processing. Hydrogen is also used as a fuel source for gas turbines and in a broad range of fuels cells to generate electricity in industrial and consumer transportation sectors.
There are several instances of pressure let down in the hydrogen distribution and consumption network where Sapphire’s FreeSpin® In-line Turboexpander (FIT) can be used to harness wasted energy.
In each of the applications mentioned below, the process of recovering energy from high pressure gas works the same. High pressure gas flows into the FreeSpin® turboexpander, the turboexpander expands the gas and generates electricity. Unlike natural gas, pure hydrogen applications do not require pre-heating and/or throttling of the gas to maintain a minimum temperature. Instead, the gas can be expanded to cryogenic temperatures. No pre-heating means no consumed fuels, which makes hydrogen expansion a decarbonization process. Hydrogen (H2), having an incredibly small mass, is prone to leak when stored and transported in pressurized equipment. The FIT eliminates potential leaks by providing a hermetically sealed environment with no dynamic seals.
Liquefaction / Gasification
Liquefaction is the process of turning gaseous hydrogen into liquid hydrogen. Liquefaction allows hydrogen to be stored in its densest state and transported with highest efficiency. Hydrogen liquefaction is achieved through a series of compression, cooling and expansion processes.
How Application Works
Hydrogen liquefaction begins with hydrogen in a gaseous state. The gas is rapidly cooled and compressed to a low temperature and a high pressure through a series of compressors and heat exchangers. Liquid nitrogen is typically used as the cooling medium. Once past its inversion point, the hydrogen gas can be cooled further through gas expansion. Expansion is achieved through a turboexpander and/or Joule-Thomson valve to convert the hydrogen to a liquid state. During the expansion process, some gaseous low temperature hydrogen is recycled to provide additional cooling to the upstream gas. Using the Sapphire FreeSpin® turboexpander system, the energy lost in expansion can be recovered and used to offset energy consumed in other areas of the liquefaction process, such as powering the compressors.
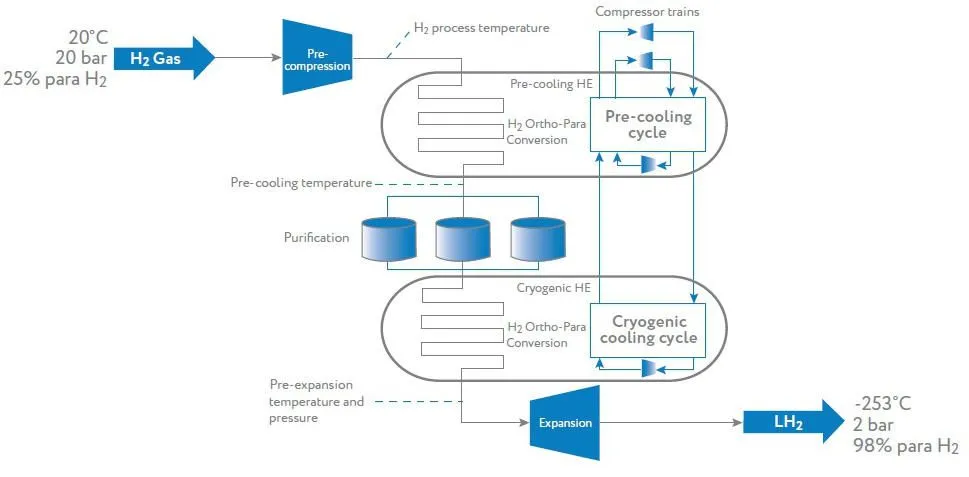
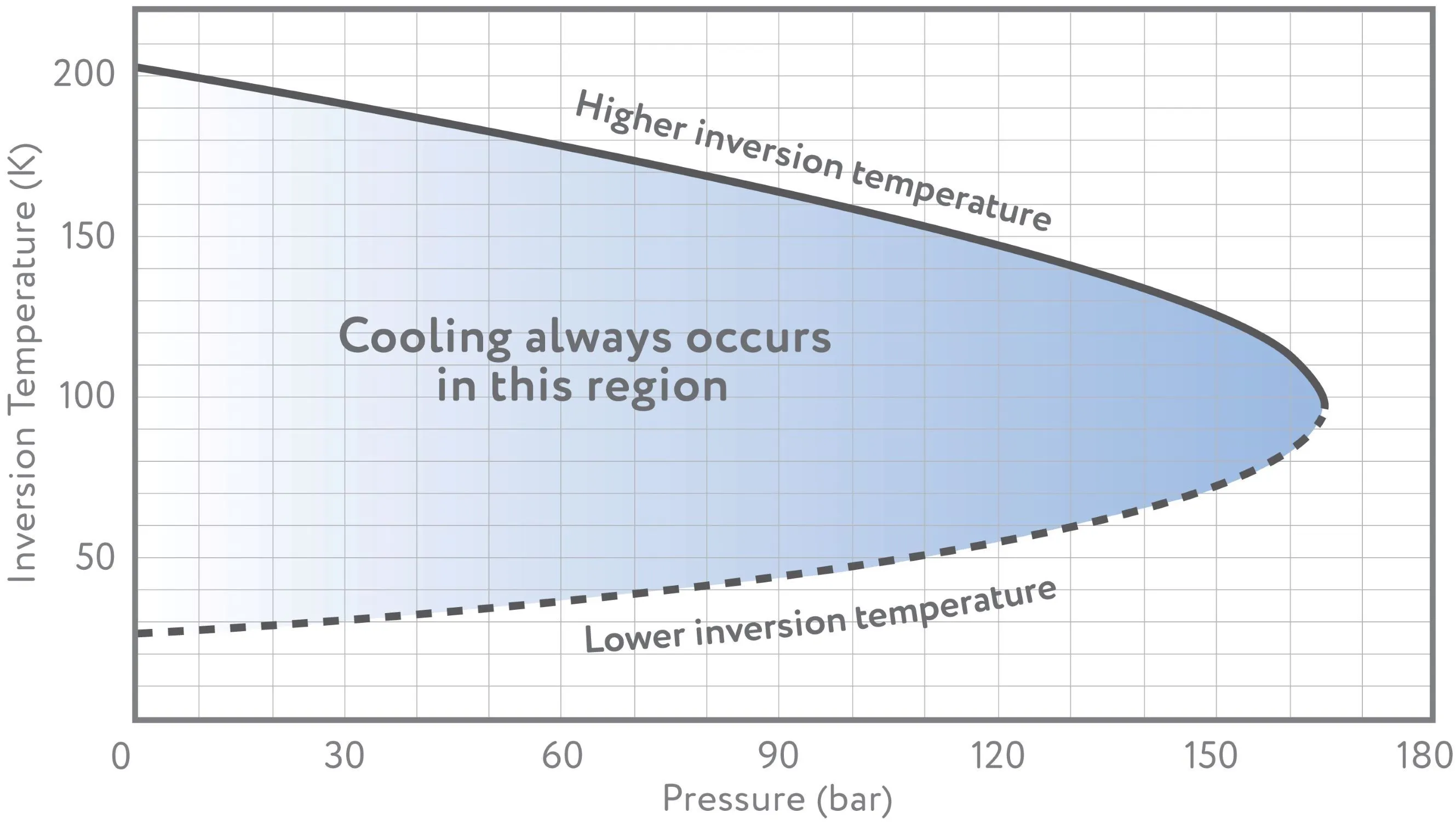
Case Study
The FIT may be used at the expansion process where the temperature and pressure of the gas has been reduced to about 96 K and 164 bar. From this point, the gas can be expanded, resulting in a 27 K and 5 bar cryogenic liquid hydrogen (LH2). Existing liquid hydrogen plants in the U.S. can produce as much as 40 tonnes per day of LH2 (the equivalent of 1667 kg/h or 18,547 Nm3/h). Through the turboexpander generator, clean electricity can be produced from these types of plants. Future LH2 plant developments call for upwards of 200 tonnes per day of LH2 production (the equivalent of 8333 kg/h or 92,713 Nm3/h), resulting in multi-megawatt power generation potential.
Pipeline Pressure Letdown
Around the world, plans are being created to implement a hydrogen distribution network via pipelines. This distribution network will be similar to that of natural gas. Hydrogen will be produced, compressed then distributed through high-capacity pipelines and delivered to city gates for further low-pressure distribution and consumption. As with natural gas, the pressure letdown (PLD) process provides an opportunity to recover stored potential energy through a turboexpander generator.
How Application Works
In this application, high pressure hydrogen gas is transported via the main pipeline and distributed through city PLD stations and further distributed to industrial and residential consumers. The high-pressure gas is typically let down through a pressure regulating valve, but in this case, the FreeSpin® turboexpander is used in parallel with a pressure regulating valve to recover pressure energy and convert it into electricity. Parallel paths are used to level load the turboexpander output during consumption transients.
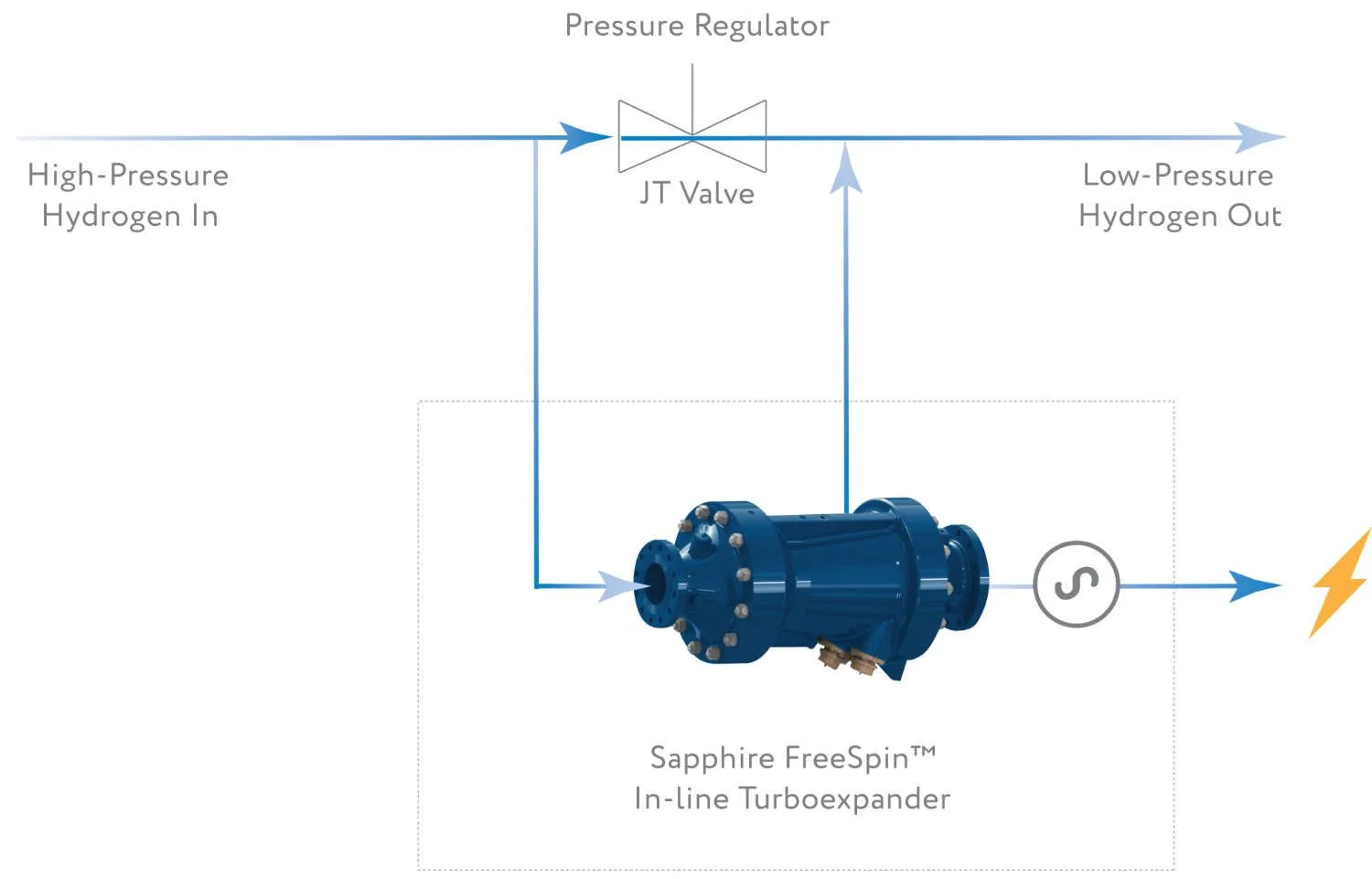
Hypothetical Case Study
Since no hydrogen pipelines have been installed yet, Sapphire can only present the following hypothetical case study based on current assumptions and natural gas experience.
Assuming the main pipeline pressure is about 400 bar, there will be several pressure letdown instances as hydrogen gas is distributed from city gates to consumers. These city gate stations may not have very high electrical requirements, and thus, the power generated may be sold to the electrical utility. If a city gate station pressure is reduced to 100 bar, the inlet temperature will be -10°C, and the flow rate 40,000 Nm3/h. At a $.04/kWh wholesale price of electricity, the 1.3 MW power potential through PLD will generate revenue of $470K USD/year.
Transport / Consumer Dispensing
Hydrogen is currently being transported in liquid and gaseous form via tanker trucks. These trucks deliver hydrogen to storage facilities, fuel stations, power plants and manufacturing facilities. In liquid form, hydrogen is kept and dispensed at cryogenic temperatures. In gaseous form, hydrogen is dispensed from the trailer’s high pressure tank to another high-pressure tank at the dispensing site.
How Application Works
As the gas is dispensed at the storage site, the pressure in the trailer drops while the pressure in the storage tank increases. This is where the FreeSpin® In-line Turboexpander can be used to recover the stored high pressure potential energy from the trailer. Eventually, the two reach a state of equilibrium, and then a compressor is needed to dispense the remaining trailer gas. Recovery of the stored energy and consumption of energy by the compressor can potentially make this application a net-zero energy process.
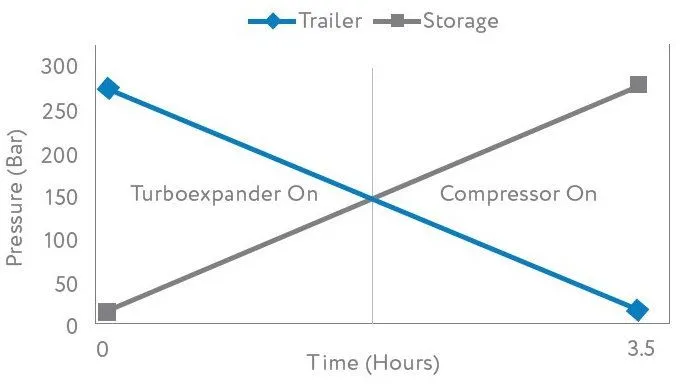
Case Study
Sapphire received pressure, temperature, and flow data of a hydrogen trailer that was emptied into a storage tank at a hydrogen filling station at a customer’s site. The initial pressure inside the trailer is 275 bar with a temperature of 60°C. The gaseous hydrogen is assumed to have an average mass flow rate of 13.1 kg/min. The assumed time to empty the trailer is 3.5 hours with the turboexpander operating during half of this time frame, while a compressor operates during the second half of the time frame to completely empty the trailer. In the situation with no turboexpander, a pressure relief valve would be used, and the expansion energy would be lost or consumed by the surrounding environment. In the second half of the cycle, a compressor consumes energy to deplete the trailer. Assuming the exit temperature of the hydrogen doesn’t drop below -41°C due to material or hardware constraints, the estimated power potential is 265 kW. Assuming this process happens five times per day at the filling station (equivalent to 17 hrs.), 1,325 kW of power per day would be recovered at this single station.
Fuel Gas (Fuel Cells & Gas Turbine Electric Power Generation)
Hydrogen fuel cell technology has allowed hydrogen production and gas turbine electric power generation to be a reversible reaction with electricity acting as the catalyst. With this concept in mind, hydrogen serves as an energy storage medium. Hydrogen will be stored in gaseous and liquid form in pressurized and cryogenic tanks, respectively. Upon energy demand, the hydrogen must be converted into electricity through a fuel gas application, such as a gas turbine or a fuel cell. Existing hydrogen gas turbines can combust up to 50% hydrogen while pure hydrogen turbines are being researched and developed.
How Application Works
In these applications, the high storage pressure (~400 bar) of hydrogen is let down to 20 to 50 bar for gas turbines and as low as .1 bar for Proton Exchange Membrane Fuel Cells. This pressure letdown (PLD) process is necessary and the Sapphire turboexpander system can help recover the energy to offset carbon emissions. The gas turbine application provides a high rate of energy return due to a typically high volumetric flow rate and 8 to 20 pressure ratio. Fuel cell applications have a low flow rate and thus less power potential, but a very high-pressure ratio, as high as 4,000.
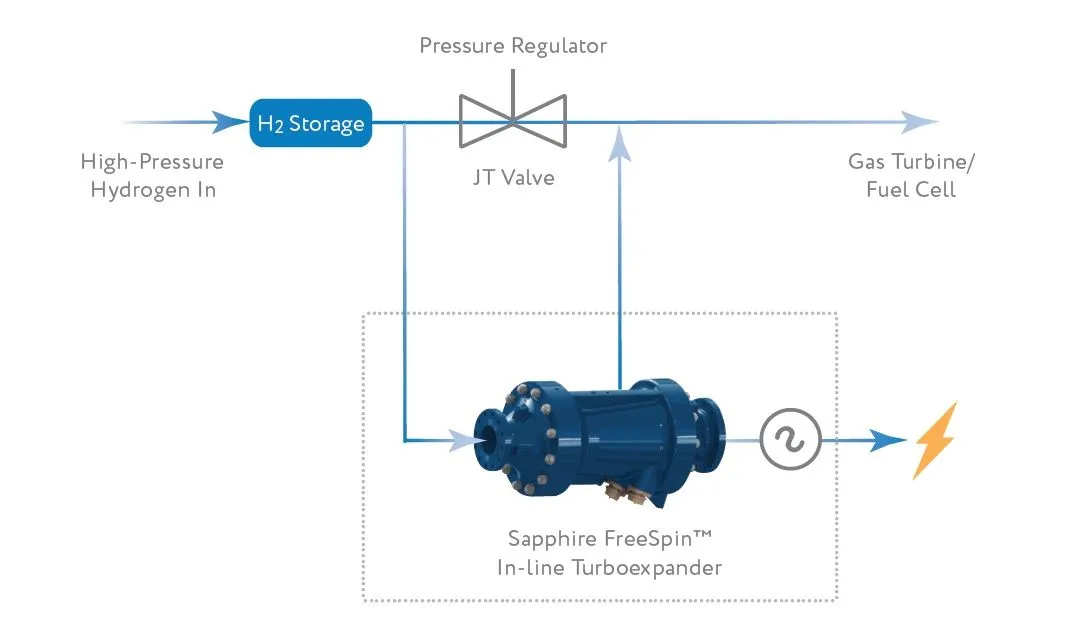
Case Study
Below is an example calculation of potential power output for a PLD fuel gas application:
- Inlet pressure: 400 bar
- Inlet temperature: 70°C
- Exit pressure: 50 bar
- Normalized volumetric flow: 11,000 Nm^3/hr
The resulting calculation for this scenario reveals an isentropic power potential of 678 kW at an exit temperature of -86°C. Recovering this power that would otherwise be lost or consumed by the immediate environment increases the efficiency of hydrogen fuel gas applications and the overall hydrogen distribution cycle.
Latest News & Upcoming Events
Additional Resources
Technical Papers
Product Brochures & Media
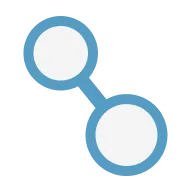
Hydrogen Gas
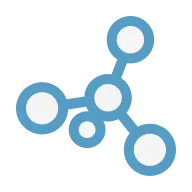